So, you’ve got a great project that involves welding brass to steel. Congratulations! Welding two different types of metal together is a challenging but rewarding process. But, it’s also important to know how to do it properly, so you don’t end up with a botched project.
Have you ever been in a situation where you needed to weld brass to steel but didn’t have the right tools or know-how? Well, fear not! This blog post will teach you how to weld brass to steel like a pro.
Whether you’re a welder by trade or just looking to fix a project at home, this guide will help you get the job done right. So read on and learn everything you know about welding brass to steel.
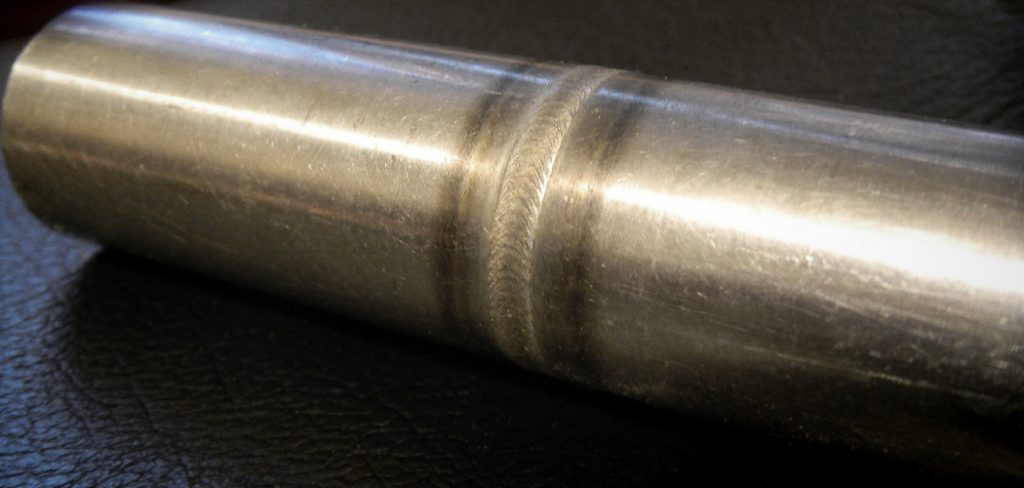
What is Welding?
Welding is a process of joining two pieces of metal together by melting and fusing them. To weld brass to steel, you must have the right equipment, supplies, and welding process knowledge.
First, you must choose the type of welding process you will use. There are two main types of welding: arc welding and oxy-fuel welding. Arc welding is the most common type of welding, and it uses an electric arc to create heat for melting the metal. Oxy-fuel welding uses a flame to melt the metal.
What is Welding Brass?
Welding is a method of joining two pieces of metal together using heat and pressure. Brass is an alloy of copper and zinc, often used for decorative purposes because of its shiny appearance. Steel is an alloy of iron and carbon, one of the most common materials used in construction and manufacturing.
What is Welding Steel?
Welding is a method of joining two pieces of metal together by heating them to a melting point and then using pressure or filler material to join them. Welding is commonly used to join steel together but can be used on other metals such as brass. Brass is softer than steel so it can be more difficult to weld. But with the proper technique, you can successfully weld brass to steel.
Tools Needed to Weld Brass to Steel
Before welding brass to steel, it is important to have all the necessary tools and safety equipment. This will help to ensure a safe and successful welding process.
- Welder
- Brass Rod or Wire
- Steel Plate
- Tungsten Electrode
- Argon Gas Bottle
- Welding Mask
- Hammer
- Chisel
- Grinder
- Pliers
10 Simple Techniques on How To Weld Brass to Steel
1. Prepare Your Materials
Brass and steel are solid and durable metals that can be welded together using the proper techniques and materials. Make sure you have a welder compatible with metals and some welding wire or rod designed explicitly for joining brass and steel. You’ll also need a clean, dust-free workspace to prevent contamination of your welds.
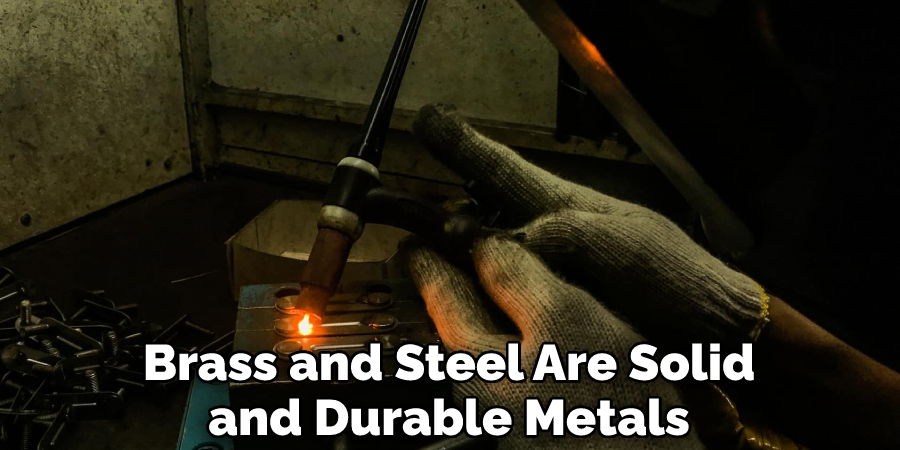
2. Clean the Surfaces of the Brass and Steel
Any dirt, grease, or other contaminants on the surface of either metal can prevent a strong bond from forming between them during welding. Use a wire brush or grinding wheel to remove any rust or paint from the surface of the metals before you begin welding.
3. Set Up Your Welder
Follow the manufacturer’s instructions to set your welder and attach the welding wire or rod. If you’re using a MIG welder, you’ll need to use Argon gas as your shielding gas to prevent contaminants from entering the weld.
4. Begin Welding at the Edge of the Brass
Hold the welding torch at a 45-degree angle and begin feeding the wire into the weld pool at the edge of the brass piece. Next, weld around the entire perimeter of the brass piece, moving slowly to ensure a strong bond between the metals.
5. Continue Welding Until Both Pieces Are Joined Together
Once you’ve gone all the way around the perimeter of both pieces, move to fill any areas where there is still space between the metals. Weld slowly and evenly until the entire area is filled in and the two pieces are joined together.
6. Let the Weld Cool
After you’ve completed welding, allow the weld to cool naturally before moving or handling it. If you try to work with the weld while it’s still hot, you could cause it to break or become weaker. Once you’re finished welding, please turn off the welder and allow the weld to cool completely before moving or handling it.
7. Inspect the Weld for Any Defects
Once the weld has cooled, you can inspect it for any defects. If there are any cracks or holes in the weld, you’ll need to re-weld that area. Look closely at the weld to check for any cracks, voids, or other defects. If you find any, re-weld that area until it’s smooth and even with the rest of the weld.
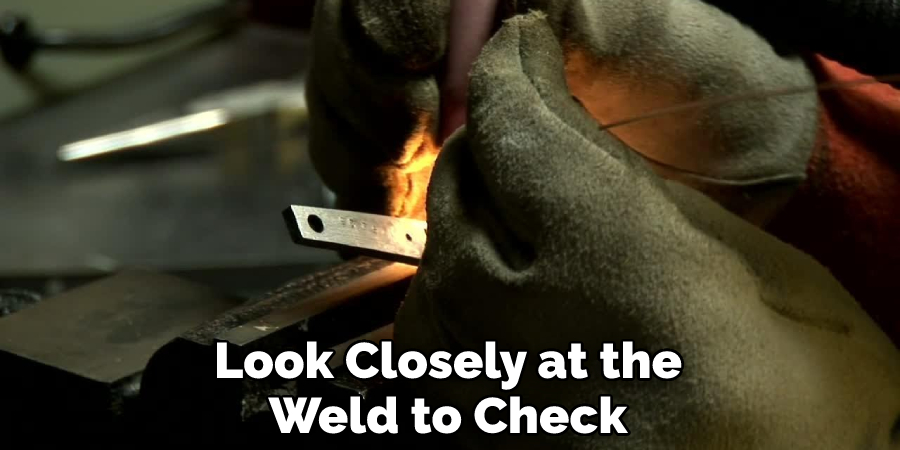
8. Grind Down Any Rough Edges
Once you’re happy with the weld, you can use a grinding wheel to smooth down any rough edges. This will help to create a professional-looking finish and help to prevent any sharp edges from causing injuries. If sharp edges or burrs are left on the weld, use a grinding wheel to remove them and create a smooth, finished surface.
9. Paint or Coat the Weld
To protect the weld from corrosion, you can paint or coat it with a clear sealant. This will also help to create a professional-looking finish. Apply the paint or sealant evenly over the weld’s entire surface, covering any cracks or voids. Allow the paint or sealant to dry completely before using or handling the weld.
10. Inspect the Weld Again
After the paint or sealant has dried, inspect the weld again to ensure no defects. If everything looks good, your weld is now complete! Congratulations, you’ve successfully welded brass to steel!
Be sure to follow all safety precautions when welding, and always wear proper safety gear, including a welding mask and gloves.
How to Know You Are Doing Wrong Brass Welding to Steel
How to Know You Are Doing Wrong Brass Welding to Steel is a critical part of the welding process.
- Welders need to be aware of the dangers of doing this wrong.
- Brass is a highly conductive metal.
- This means that it can easily cause an electric shock.
- Also, brass is a very soft metal.
- This makes it easy to melt and distort.
- As a result, it is crucial to use the correct techniques when welding brass to steel.
- If unsure about the techniques, you should ask a professional welder for help.
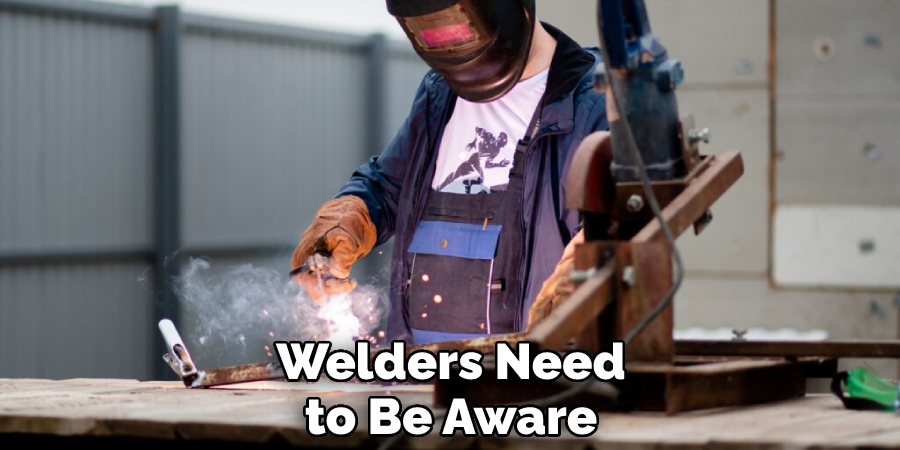
10 Necessary Precautions on How to Weld Brass to Steel
1. Use the Correct Welding Process
When welding brass to steel, it is essential to use the correct welding process to avoid potential problems. The two most common processes for welding these metals are gas tungsten arc welding (GTAW) and gas metal arc welding (GMAW).
2. Use the Correct Filler Material
When welding brass to steel, it is essential to use the correct filler material to avoid potential problems. The two most common materials used for welding these metals are bronze and nickel.
3. Use the Correct Electrode
When welding brass to steel, it is essential to use the correct electrode to avoid potential problems. Tungsten and Hafnium are the two most common electrodes used for welding these metals together.
4. Use the Correct Shielding Gas
When welding brass to steel, it is essential to use the correct shielding gas to avoid potential problems. Argon and Helium are the two most common gases used for welding these metals together.
5. Use the Correct Wire
When welding brass to steel, it is essential to use the correct wire to avoid potential problems. Copper and nickel are the two most common wires used for welding these metals together.
6. Clean the Materials Before Welding
It is essential to clean the materials before welding them together to avoid any potential problems. Chemical cleaning and sandblasting are the two most common methods used for cleaning these metals before welding.
7. Preheat the Materials Before Welding
It is also essential to preheat the materials before welding them together to avoid any potential problems. Torch heating and induction heating are the two most common methods used for preheating these metals before weldings.
8. Post-weld Heat Treatment
After welding brass to steel, it is essential to perform post-weld heat treatment to avoid potential problems. The two most common methods used for post-weld heat treatment are stress relieving and annealing.
9. Use the Correct Cooling Method
When welding brass to steel, it is important to use the correct cooling method to avoid potential problems. Air cooling and water cooling are the two most common methods for cooling these metals after welding.
10. Inspect the Welds Regularly
It is very important to inspect the welds regularly to ensure they are of good quality and free of defects. The two most common methods used for inspecting welds are visual inspection and non-destructive testing.
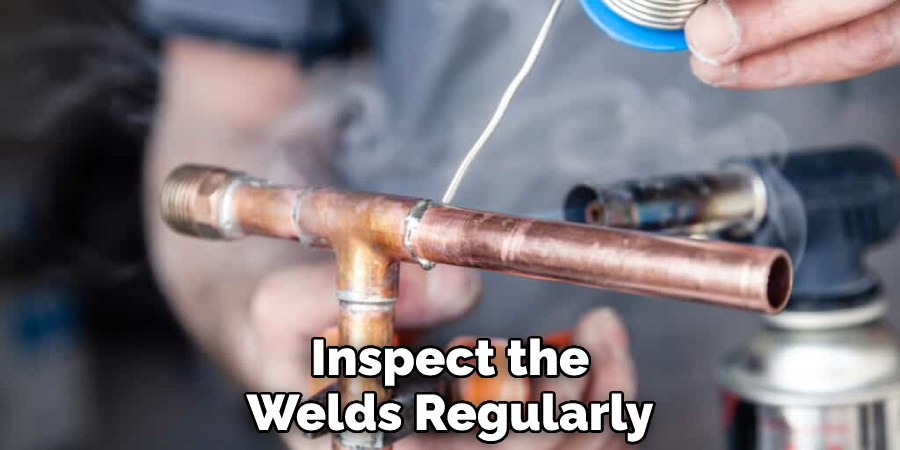
Conclusion
So, there you have it. Welding brass to steel is a fairly simple process requiring a few basic supplies and some practice. First, clean the surfaces of both the brass and steel that will be joined. Next, apply a layer of welding flux to both surfaces.
Then, use a MIG welder to weld the two pieces together. Finally, remove any excess welding material and allow the joint to cool.
By following these steps and using the right techniques, you should know how to weld brass to steel. Have you ever tried welding brass to steel? What tips would you add? Let us know in the comments!
You May Also Read: How to Test Rca Inputs on Amp
Occupation: Expert in Hardware Tools
Education: Bachelor’s Degree in Mechanical Engineering
Profile:
Enrique Howard is a seasoned expert in the field of hardware tools, with a robust background in mechanical engineering that underpins his extensive knowledge and skills. Holding a degree in mechanical engineering, Enrique has cultivated a deep understanding of tool design, mechanics, and the intricacies of various hardware applications. His educational foundation empowers him to innovate and refine tools that enhance efficiency and effectiveness in a wide range of industries.
Professional Focus:
Enrique’s professional focus encompasses a diverse array of areas within the hardware tools sector, including:
- Tool Design and Development: Leveraging his engineering expertise, Enrique specializes in designing tools that meet specific user needs, ensuring optimal performance and durability.
- Material Science: Understanding the properties of various materials allows him to recommend the best tools for specific applications, enhancing safety and efficiency.
- Ergonomics: He emphasizes the importance of ergonomic design in tools, striving to create solutions that reduce user fatigue and improve comfort during prolonged use.
- Sustainability: Enrique is committed to promoting environmentally friendly practices in tool manufacturing, advocating for the use of sustainable materials and processes.
- Education and Training: Through workshops, seminars, and written content, he focuses on educating both professionals and DIY enthusiasts about tool selection, maintenance, and safe usage practices.
Throughout his career, Enrique has worked on numerous projects, collaborating with manufacturers and craftsmen to develop cutting-edge hardware solutions. His expertise spans from traditional hand tools to advanced power tools, allowing him to contribute significantly to both professional and DIY communities.
As an author, Enrique shares his insights through articles, guides, and tutorials, aimed at helping enthusiasts and professionals alike navigate the complexities of hardware tools. His passion for education and practical application drives him to continually explore new technologies and methodologies, making him a trusted voice in the hardware industry.
Whether he’s writing about the latest tool advancements or providing practical tips for tool maintenance, Enrique Howard is dedicated to empowering others with the knowledge and skills necessary to excel in their hardware endeavors.