Sharpening your carbide lathe tools can make an enormous difference in the quality of your finished work. It’s important to have a sharp cutting edge for optimal performance and longevity, but it isn’t always easy or obvious what needs to be done in order to achieve this.
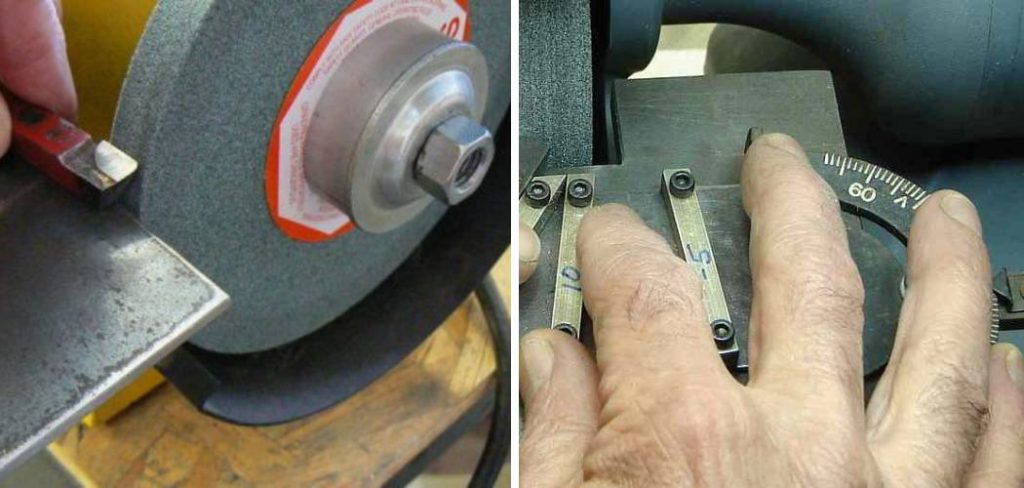
In this blog post, we’ll provide step-by-step instructions on how to sharpen carbide lathe tools in order to get excellent results each time. Keep reading if you’re looking for advice from professional machinists who know just exactly how to make your tools look and perform their best!
The Importance of Maintaining Sharp Carbide Lathe Tools for Optimal Performance
Maintaining sharp carbide lathe tools is crucial for achieving optimal performance from your lathe machines. Not only does sharpening the tool ensure that it is able to cut more effectively, but it also helps reduce wear and tear on the tool itself, making it last longer overall.
It can also help improve safety in the workplace as a sharper tool will be less likely to cause kickback or other unexpected movements that can harm the operator and those in the vicinity.
Sharp carbide lathe tools should also produce a better finish on the material being cut, which can be important for certain manufacturing processes. In addition, sharpening tools regularly ensures that they don’t become too worn down and require costly replacement.
To get the most out of your carbide lathe tools, it is essential to sharpen them regularly using an appropriate tool grinder or sharpening stone designed for use with carbide tools. Different types of materials will require different techniques for sharpening, so make sure to follow manufacturer instructions closely when doing so.
Proper maintenance of these tools not only helps ensure that you get optimal performance but also extends the life of your tools and helps keep your shop running efficiently.
Benefits of Proper Sharpening in Achieving Precise and Efficient Lathe Work
Sharpening a lathe’s carbide cutting tools is an essential part of achieving precise and efficient results in your work. A properly sharpened tool allows you to make precise cuts with minimal effort and decreases the amount of time required for a job.
It also reduces the occurrence of “tearing” or “chattering,” where the cutting edge of the tool scrapes against the workpiece as it rotates, causing uneven wear to both the tool and workpiece. With a sharpened lathe carbide tool, you can get smoother, more accurate results in less time.
Additionally, properly sharpening your lathe tools helps improve their longevity. The sharper an edge is, the longer it will hold its shape. This means that you won’t need to replace dulled tools as frequently and can save money in maintenance costs over time.
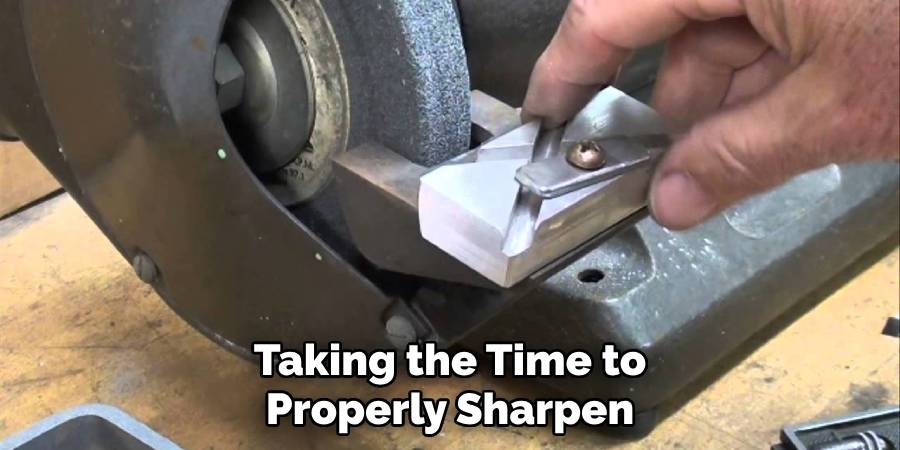
When using new tools or resharpening old ones, the process should be done with precision and accuracy to ensure their optimal performance.
Overall, sharpening your lathe carbide tools is a necessary step in achieving high-quality, precise results from your work. Taking the time to properly sharpen and maintain your tools can pay off in more efficient production times and less money spent on maintenance costs.
Types of Carbide Lathe Tools
- Carbide inserts
- Carbide-tipped tools
- Solid carbide tools
Anatomy of Carbide Lathe Tools
- Carbide insert or tip
- Shank or holder
- Tool rest and handle (if applicable)
10 Steps How to Sharpen Carbide Lathe Tools
Step 1: Assess Tool Condition
Before sharpening your carbide lathe tools, assess their condition. Look for signs of dullness or damage, such as chipping or uneven cutting edges. Identifying specific areas that require sharpening will help you focus your efforts effectively.
Step 2: Gather Sharpening Supplies
To sharpen carbide lathe tools, gather the necessary supplies. You will need a diamond wheel or grinding stone, a tool rest or jig for stability, safety goggles, a sharpening compound or coolant, and a cloth or towel for cleaning.
Step 3: Secure the Tool Rest or Jig
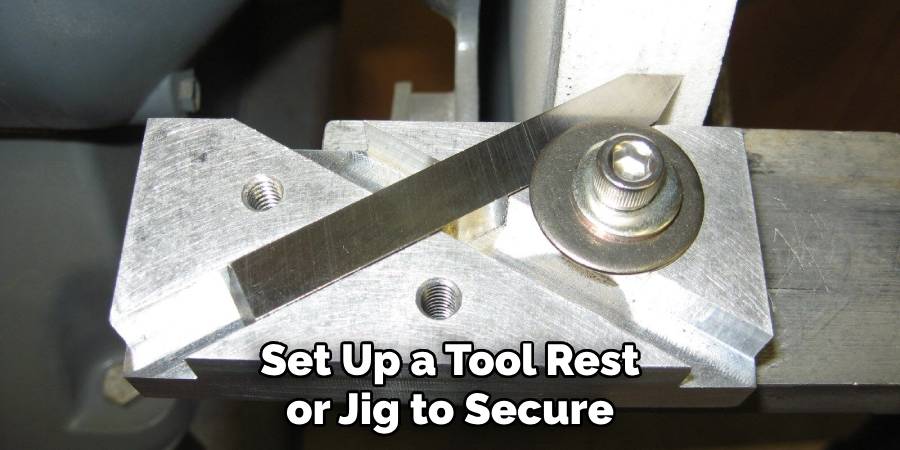
Set up a tool rest or jig to secure the carbide lathe tool during sharpening. This provides stability and control throughout the sharpening process, ensuring consistent and accurate results. The sharpening jig should be set up with the correct angle for the specific tool being sharpened. Once in place, securely tighten it to a surface that can withstand the pressure of sharpening.
Step 4: Safety Precautions
Prioritize safety when sharpening carbide lathe tools. Wear safety goggles to protect your eyes from any debris. Ensure that the grinding area is well-ventilated and follow all safety guidelines provided by the manufacturer. Use the grinder at a slow speed, and ensure not to press down too hard on the tool so that it does not overheat.
Step 5: Establish the Grinding Angle
Determine the appropriate grinding angle for your specific carbide lathe tool. Refer to the manufacturer’s recommendations or consult a sharpening guide. Carbide tools typically require a specific angle for optimal cutting performance.
Step 6: Grinding the Cutting Edge
Position the carbide lathe tool on the grinding wheel at the established grinding angle. With controlled and consistent pressure, move the tool across the wheel in a smooth and sweeping motion. Ensure the entire cutting edge comes into contact with the wheel during each pass.
Step 7: Coolant or Sharpening Compound
To prevent overheating and maintain cutting efficiency, apply a coolant or sharpening compound to the carbide lathe tool during sharpening. This helps dissipate heat and provides lubrication for smoother grinding.
Step 8: Inspect and Test the Edge
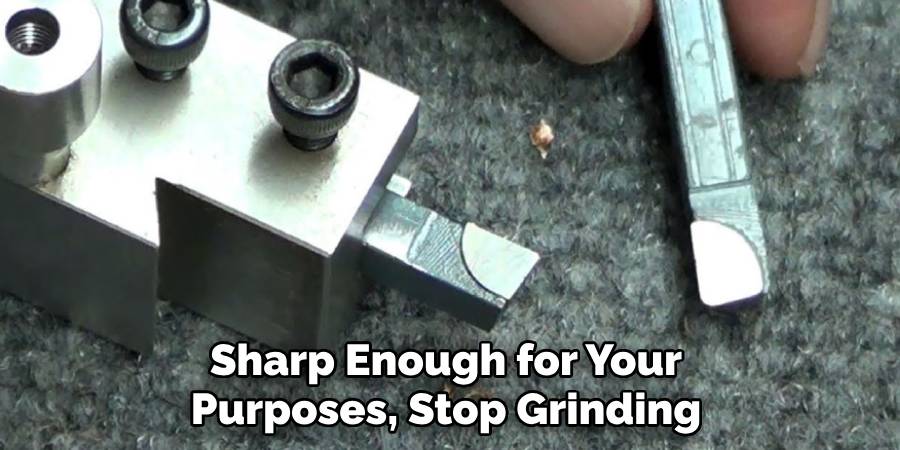
Periodically inspect the cutting edge during sharpening. Look for signs of improvement, such as a clean and sharp edge. Stop grinding and test the tool on a scrap piece of material to assess its cutting performance. Adjust as necessary. Once the edge is sharp enough for your purposes, stop grinding.
Step 9: Honing and Polishing
After grinding, consider honing and polishing the carbide lathe tool for a refined cutting edge. Use a diamond honing stone or sharpening compound to remove any burrs or roughness and achieve a polished finish.
Step 10: Cleaning and Maintenance
After sharpening, clean the carbide lathe tool thoroughly to remove any grinding residue or coolant. Use a cloth or towel to wipe away debris, ensuring the tool is clean and ready for use. Properly store the tool in a dry and safe location.
Things to Consider When Sharpening Carbide Lathe Tools
When sharpening carbide lathe tools, it is important to consider a few key points in order to ensure that the tool performs optimally and has a long life. Here are some of the most important things to think about before beginning the sharpening process:
1. Tool Material:
Be sure to determine the material of your tool before you sharpen it. Carbide tools are often made from tungsten, titanium, or other hard metals and alloys. It is important to use the right sharpening technique for the specific material of your tool in order to get the best results.
2. Shape:
The shape of carbide lathe tools can vary greatly depending on their purpose so be sure that you understand what type of shape works best with your project before beginning to sharpen. For instance, rounded edges are used for turning softer materials while sharper edges may be needed for harder materials.
3. Angle:
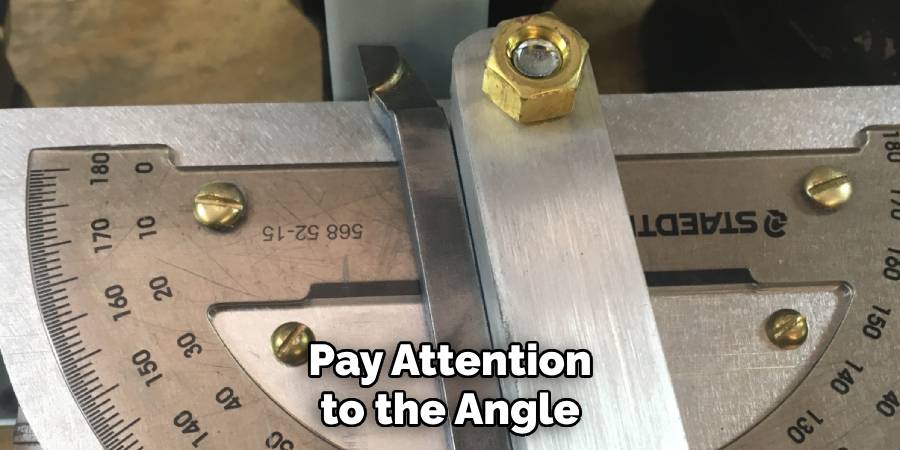
When sharpening a carbide lathe tool, you need to pay attention to the angle at which you hold the tool against the sharpening stone. Different angles may be needed depending on the type of material being cut and the shape of your tool, so make sure to take this into account when sharpening.
4. Heat:
Sharpening a carbide lathe tool can cause it to become very hot which can reduce its longevity. To avoid this, always use a coolant or lubricant when sharpening and take breaks regularly to allow the tool to cool down before continuing with the process.
By taking all of these considerations into account you should have no problem getting your carbide lathe tools nice and sharp for any job! Keep in mind that proper care and maintenance are key to ensuring that your tools will remain in top condition for years to come.
Conclusion
Now that you have read this blog post about how to sharpen carbide lathe tools, you have all the know-how you need! Like most endeavors, sharpening carbide lathe tools is all about careful preparation and safe practices. Make sure to take it slow and carefully feel for a wire edge before running your tool through at full speed.
With all these tips in mind, you can confidently sharpen your own lathe tools with no fear of ruining them. Skillfully crafted tools can make all the difference when it comes to crafting wood pieces, furniture, or cabinetry—remember that if you run into any trouble while sharpening your lathe tools, there are always professionals available for advice and guidance.
After all, one of the greatest aspects of DIY projects is learning to sharpen and care for our own tools – so what are you waiting for? Gather up your grinders and safety gear now; it’s time to start sharpening those carbide lathe tools!
Occupation: Expert in Hardware Tools
Education: Bachelor’s Degree in Mechanical Engineering
Profile:
Enrique Howard is a seasoned expert in the field of hardware tools, with a robust background in mechanical engineering that underpins his extensive knowledge and skills. Holding a degree in mechanical engineering, Enrique has cultivated a deep understanding of tool design, mechanics, and the intricacies of various hardware applications. His educational foundation empowers him to innovate and refine tools that enhance efficiency and effectiveness in a wide range of industries.
Professional Focus:
Enrique’s professional focus encompasses a diverse array of areas within the hardware tools sector, including:
- Tool Design and Development: Leveraging his engineering expertise, Enrique specializes in designing tools that meet specific user needs, ensuring optimal performance and durability.
- Material Science: Understanding the properties of various materials allows him to recommend the best tools for specific applications, enhancing safety and efficiency.
- Ergonomics: He emphasizes the importance of ergonomic design in tools, striving to create solutions that reduce user fatigue and improve comfort during prolonged use.
- Sustainability: Enrique is committed to promoting environmentally friendly practices in tool manufacturing, advocating for the use of sustainable materials and processes.
- Education and Training: Through workshops, seminars, and written content, he focuses on educating both professionals and DIY enthusiasts about tool selection, maintenance, and safe usage practices.
Throughout his career, Enrique has worked on numerous projects, collaborating with manufacturers and craftsmen to develop cutting-edge hardware solutions. His expertise spans from traditional hand tools to advanced power tools, allowing him to contribute significantly to both professional and DIY communities.
As an author, Enrique shares his insights through articles, guides, and tutorials, aimed at helping enthusiasts and professionals alike navigate the complexities of hardware tools. His passion for education and practical application drives him to continually explore new technologies and methodologies, making him a trusted voice in the hardware industry.
Whether he’s writing about the latest tool advancements or providing practical tips for tool maintenance, Enrique Howard is dedicated to empowering others with the knowledge and skills necessary to excel in their hardware endeavors.