Do you need to grease parts but don’t know how to efficiently get the air out of your grease gun? Are you unable to find the correct instructions that will help free packed-in air from your tool’s system and get those beans of lubrication flowing again? It is important to know how to get air out of a grease gun.
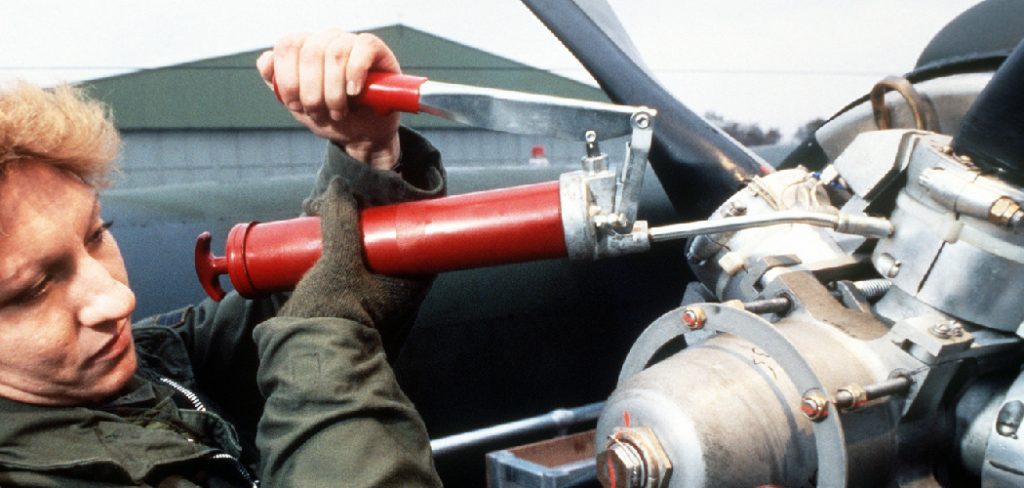
Well, there’s no need to worry – we have all the steps covered for you on how to effectively remove trapped air from a grease gun for continued operation. Most problems with faulty output can be solved after correctly eliminating excess or frozen air in the handgun.
With this detailed guide, learn preventative measures as well as troubleshooting tips so you can stay one step ahead when it comes time to perform maintenance tasks!
Tools You Will Need
- Grease gun
- Funnel
- Clean cloths
- Barrel wrench (optional)
- Grease cartridge container or suitable grease reservoir
- Suitable lubricant for your application/parts
8 Steps on How to Get Air Out of a Grease Gun
1. Locate the Plunger
Removing the barrel or body of a grease gun can be done easily with a few simple tools. Begin by disconnecting the air hose and other attachments from the grease gun. After that, you’ll want to unscrew the two threaded joints located on either side of the barrel, which will effectively separate it from its body or frame.
This will leave you with just the plunger exposed, which is vital for getting air out of your grease gun before you fill it up with fresh lubricant.
By manually pushing down on the plunger and using a wretch to slowly turn it towards 90 degrees, you’ll compress the remaining air in the chamber so more grease can fit inside for better performance when using your gun. As long as you follow these steps carefully and precisely, you should be able to get the air out of a grease gun quickly and efficiently.
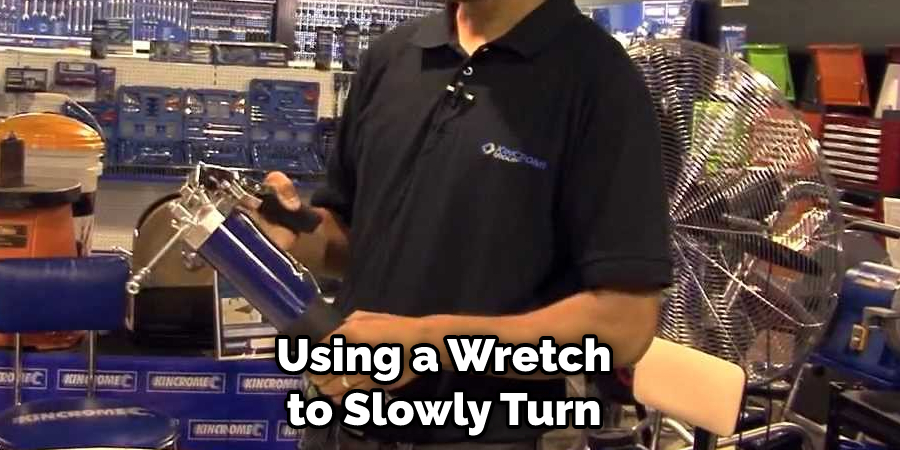
2. Inspect the O-ring
Inspecting the O-ring on a grease gun plunger is an essential part of keeping it in good working condition. O-rings wear down over time and can crack or become brittle due to repeated use. When this happens it can cause a leak, which will make it difficult to get the air out of a grease gun.
To avoid this, check the O-ring regularly for any signs of wear, tear or cracking and replace it immediately if necessary. Replacing worn O-rings regularly can help ensure that your grease gun operates at its best and remains free of air bubbles and other blockages.
3. Attach a Suitable Lubricant Reservoir or Cartridge
Using a grease gun can be a challenging task, especially if air gets trapped in the barrel. To avoid this, it’s important to attach the proper lubricant reservoir or cartridge to the barrel before re-assembling it back onto the body of the grease gun. This will ensure that no air is trapped inside.
Additionally, making sure that all connections are securely tightened is also important as otherwise, you may experience issues with reaching and maintaining ideal pressure when using your grease gun. Following these simple steps can lead to a better and more efficient lubrication process for your equipment and machinery.
4. Use a Funnel and Slowly Fill the Barrel
Greasing your vehicle or tool is an essential part of regular maintenance and upkeep. To ensure your grease gun is working properly, it’s important to get any air bubbles out before you begin using it. A safe, easy way to do this is to use a funnel and slowly pour the grease in until you’ve reached the top of the barrel.
Before using your gun, place a rag over the tip of the nozzle to catch any excess grease which may come out as you’re pushing in the plunger handle. This method should allow for more efficient and accurate dispensing of products with far less mess.
5. Place a Cloth Underneath
If your grease gun isn’t pumping out the way it should, one of the first steps you can take to troubleshoot is to get the air out of the barrel. This can normally be accomplished by carefully placing a cloth underneath and then gently tapping the side of the gun with either a hammer or wrench.
In this way, you can usually release any trapped air that may have built up inside along the walls of your grease gun’s barrel which should help to restore normal functionality. If this doesn’t do the trick, you may need to use an alternate method such as inserting an adhesive strip at one end. It’s also a good idea to make sure that your nozzle is clean and clear prior to attempting any type of repair.
6. Wipe Off any Excess Lubricant
Fully reassembling a gun is the most important step when trying to get the air out of a grease gun. Start by replacing any parts that may have been taken apart. Make sure you are using the correct parts, as this can make all the difference between successful maintenance and an unreliable product. Once all the parts are in place, use a cloth to wipe off any excess lubricant present on the outside of the barrel.
Doing this helps ensure that no extra dirt or debris clogs the barrel or otherwise interferes with normal operation. It is possible to use other materials for wiping, but it’s always good practice to avoid anything rough or abrasive that can potentially impact performance and longevity negatively.
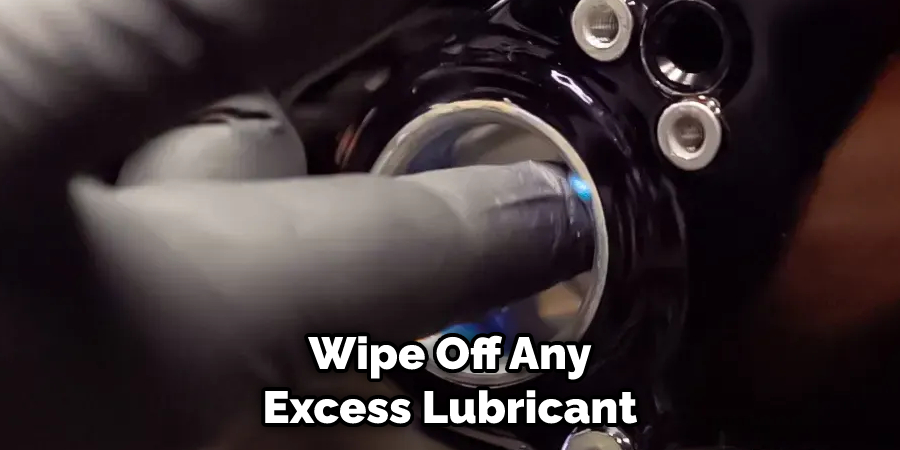
7. Pump the Trigger Several Times
Greasing a machine with a grease gun can be an intimidating process, but if you follow the proper steps it can be easy and get the job done correctly. When it comes to getting air out of your grease gun, start by inserting the appropriate grease fitting into the grease nipple on the machine that needs to be greased.
Then operate the catch trigger of your grease gun a few times without pumping to break any built-up air pressure. Finally, pump the hand trigger of your grease gun several times until you released air bubbles coming from a special vent hole in your handle. Once no more bubbles of air come out, you are ready to inject high-quality lubrication into your components and give them increased life spans!
8. Place your Gun in an Upright Position
When you want to make sure all air has been released from a grease gun, the proper technique should always be used. Start by making sure your grease gun is in an upright position and then press the trigger to release any lubricant that may be present.
Carefully observe the lubricant being expelled from the nozzle and make sure no air is leaving along with it. If you notice some air entering into it, you can depress the plunger several times until only lubricant is coming out of it. Having a grease gun with no air inside allows for an even distribution of lubricant and leaves your machinery running smoothly. Once removed, your grease gun is now ready to use.
Following these steps will help you get the air out of your grease gun and set it up for successful operation. If after following these instructions, you still experience difficulties with the output of your tool, consider consulting a professional for further guidance. Enjoy greasing away with zero worries!
10 Preventative Tips
- Ensure a snug fit when attaching the grease gun to your reservoir or cartridge container
- Inspect your O-ring for cracks and replace it if needed
- Clean out any residue that remains in the barrel of your gun after use
- Use light taps with a hammer to help remove air pockets from within the barrel
- Do not overfill your gun with grease – only fill up to the designated line within the barrel
- Grease all parts before reassembling them back together
- Place a cloth underneath when tapping your gun to help prevent any damage
- Check that all connections are secure after each use
- Make sure to clean your grease gun and all its components before storage
- Store your grease gun in a dry, cool place for optimal usage.
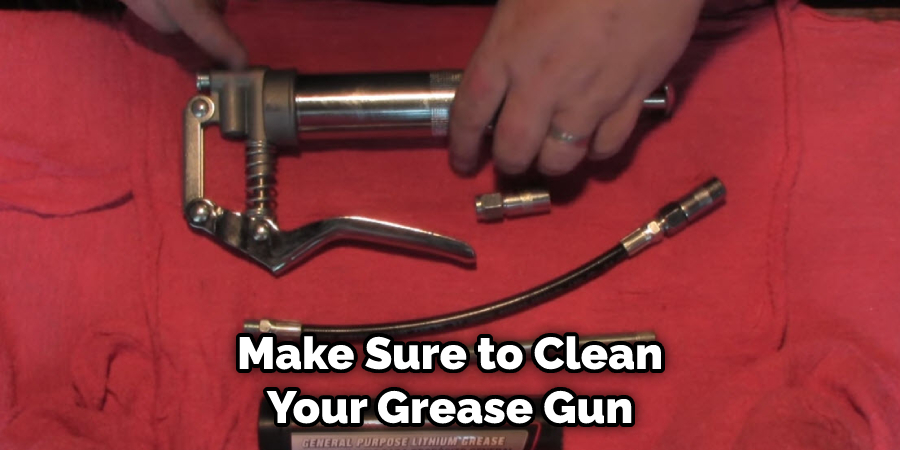
By following these steps to Get Air Out of a Grease Gun, you can ensure that your tool is running smoothly and efficiently, with no disruption when it comes time to grease parts. With these preventative and troubleshooting tips, you’ll be able to make sure your gun is operating in top condition for years to come!
Unclog Your Grease Gun: A Comprehensive Guide
Unclogging a grease gun can be a tricky procedure that requires knowledge of the workings of the gun and the correct tools to get it cleared out. If you are having difficulty with your gun, this guide can help you understand what needs to be done to successfully unclog it.
You will need items like cleaning wipes, paper towels, and solvent or WD-40 to clear the gun of any obstructions. Begin by removing everything from the nozzle, including excess grease and dirt deposits.
Next, submerge the nozzle into some warm water and clean it thoroughly with a soft cloth or brush. Afterward, open up the handle of the weapon and remove all leftover particles that may have been clogging up the mechanism.
Finally, apply a few drops of solvent or WD-40 on a rag and run it along each piston rod until they slide freely once more – ensuring that every nook and cranny is free from debris. With these steps followed carefully, your grease gun will be back in pristine condition in no time.
How To Extend The Life Of your Grease Gun: Proven Strategies
Replacing your grease gun regularly can be expensive, so it’s important to try and ensure that you are getting the longest life possible out of it. To extend the life of your grease gun, start with regular cleaning and maintenance. Ensure that the pressure relief valve is functioning properly and that the nozzle is free from dirt and debris.
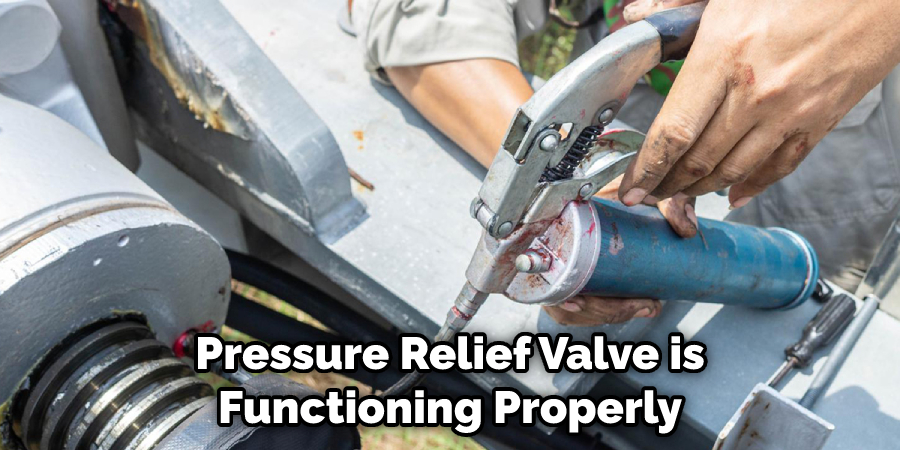
Additionally, replacing any worn-out seals or O-rings can prevent any future leaks which will shorten the lifespan of your grease gun. Make sure to use only recommended lubricants for your type of grease gun to maximize its longevity as well. Following these tips should help extend the useful life of your grease gun so you don’t have to go through frequent replacements.
You Can Also Check It Out Prevent Snow from Sticking to Shovel
Conclusion
If your grease gun has been sitting for a while, it’s probably full of air. You should carefully determine how to get air out of a grease gun. To get the air out, simply remove the cap and pump the handle until you see grease coming out of the nozzle.
If you’re still having trouble after doing this, try bleeding the line by loosening the screw on the bottom of the gun. Once you’ve bled the line, your grease gun should be good to go!