A crank sensor, otherwise known as a crankshaft position sensor, is an essential part of your car’s engine. This sensor determines the position and speed of the crankshaft. If your car’s engine is not running correctly, it may be because your crank sensor is broken.
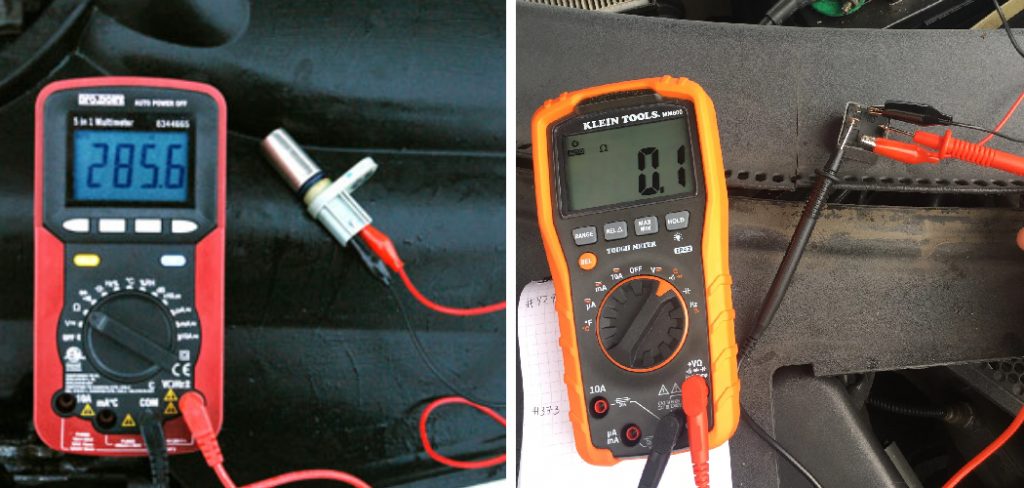
With a multimeter, it’s easy to test the resistance levels at the crank sensor connector to see if there is any problem. This blog post will show you how to check crank sensor with multimeter. We will also provide tips on fixing a broken crank sensor. Read on for more information.
What is a Crankshaft Sensor?
The crankshaft sensor is an important engine management component near the crankshaft pulley. Its function is to monitor the crankshaft’s position and speed and send this information to the engine control unit (ECU). The ECU then uses this data to control ignition timing and fuel injection. If the crankshaft sensor is not working properly, the engine will not run smoothly and may even stall. In some cases, the check engine light will come on.
Why Should You Check Crank Sensor?
The most common reason to check your vehicle’s crankshaft sensor is that the “check engine” or “service engine soon” light is on. Another reason to check your crankshaft sensor is if your car is having difficulty starting or if it’s frequently stalling. If you notice any of these issues, it’s time to test your crankshaft sensor with a multimeter.
You’re looking for resistance and voltage when checking the crankshaft sensor with a multimeter. The crankshaft sensor produces a small amount of voltage when it’s working properly, and this voltage should remain steady while the engine is running. If the multimeter reading fluctuates or there is no voltage, the crankshaft sensor is likely defective.
What Tools & Supplies You’ll Need?
To check your car’s crankshaft sensor, you’ll need the following tools and supplies:
A Multimeter
A multimeter is an essential tool for checking electrical circuits. It measures voltage, current, and resistance in DC and AC circuits.
Safety Gear
Always wear safety gear when working on your vehicle, such as protective glasses and gloves.
A Vehicle Repair Manual
A vehicle repair manual is a helpful resource for locating the crankshaft sensor and understanding its wiring diagram. It will also provide you with the correct resistance values for your specific vehicle.
A Friend (Optional)
While it’s possible to check the crankshaft sensor on your own, having a friend assist can be helpful. One person can operate the car while the other uses the multimeter to read the voltage and resistance levels. This can make the process more efficient and accurate.
Step by Step Instructions: How to Check Crank Sensor With Multimeter
Step 1: Test the Multimeter
Before testing the crankshaft sensor, it’s important to test the multimeter. To do this, touch the multimeter leads together and check that the reading is 0 ohms. If it’s not, the multimeter is not working properly, and you’ll need a new one. If you’re unsure how to use a multimeter, check out this blog post.
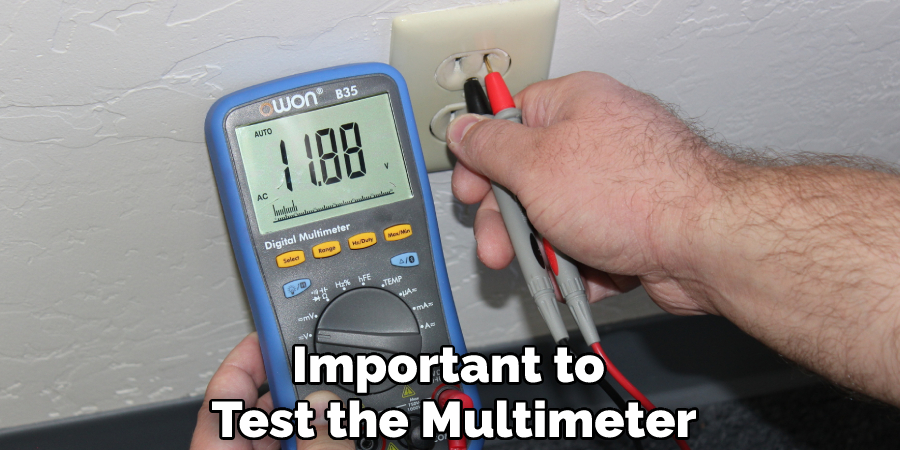
It’s also essential to set the multimeter to the appropriate settings for testing resistance and voltage. Refer to your vehicle’s repair manual for specific instructions.
Step 2: Find the Crankshaft Sensor
The crankshaft sensor is usually located near the crankshaft pulley or on the engine block. It’s fairly easy to access in most cars. However, you may need to remove a few parts on some cars to get to it. Consult your car’s service manual for specific instructions.
You should also check the wiring harness and connector for any visible damage, such as corrosion or loose connections. If you notice any issues, these will need to be addressed before proceeding.
Step 3: Disconnect the Crankshaft Sensor
Once you’ve located the crankshaft sensor, you’ll need to disconnect it from the wiring harness. On most cars, this is simply a matter of unplugging it. However, some cars may require removing a few bolts to access the wiring harness. If you want to avoid damaging the wiring harness, it’s best to consult your car’s service manual.
It’s also important to note that on some cars, the crankshaft sensor may be connected to other components. In this case, you’ll need to disconnect these components before testing the sensor.
Step 4: Set the Multimeter to Ohms
Once you’ve disconnected the crankshaft sensor from the wiring harness, you’ll need to set the multimeter to ohms. This is usually done by turning the knob until it points to the Ω symbol. You can use the resistance setting if your multimeter doesn’t have an ohms setting.
But first, you need to check the resistance level of your crankshaft sensor. Refer to your vehicle’s repair manual for the correct value. Typically, a good crankshaft sensor should have a resistance between 500 and 900 ohms.
Step 5: Check the Resistance
With the multimeter set to ohms, touch the leads to the sensor’s terminals. You should see a reading of about 1-2 ohms. The sensor is most likely defective if the reading is much higher or lower than this. If your sensor is defective, you’ll need to replace it.
You should also check the resistance of the wiring harness by touching one lead to the sensor’s terminal and the other lead to a ground source. If you get an infinite reading, there is a break in the wiring and it will need to be repaired.
Step 6: Set the Multimeter to AC Volts
Once you’ve checked the resistance, you’ll need to set the multimeter to AC volts. This is usually done by turning the knob until it points to the VAC symbol. You may need to press a button on some multimeters to switch between AC and DC voltage measurements.
It’s important to note that some crankshaft sensors produce a square wave voltage signal, so you may need to set your multimeter to read this type of signal.
Step 7: Connect the Leads to the Crank Sensor
Connect the leads to the crank sensor with the multimeter set to AC volts. The positive lead (red) should be attached to the signal wire, and the negative lead (black) should be attached to the ground. Consult your car’s service manual if you’re unsure which wire it is. When connecting the leads, ensure to avoid touching any other wires, as this can cause damage to the sensor.
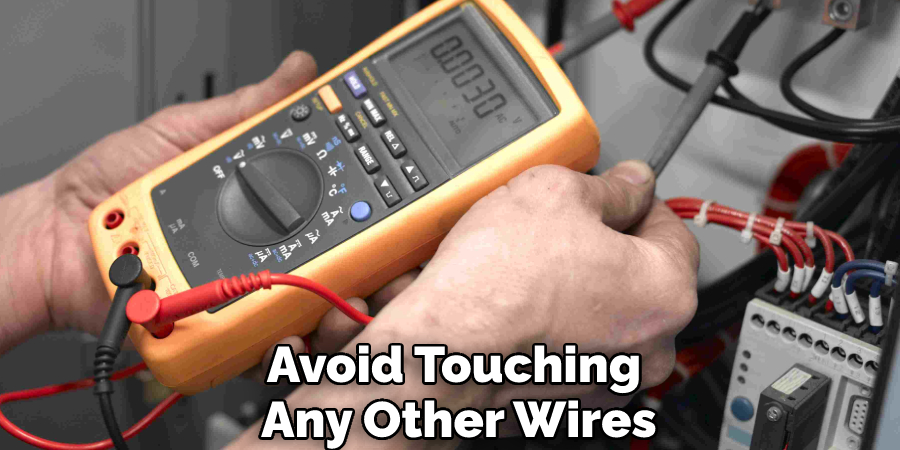
You can now start the engine and check the voltage reading on the multimeter. A healthy crankshaft sensor should produce a steady voltage while the engine is running. If you get a fluctuating or low voltage reading, the sensor is likely defective.
Step 8: Check the Voltage
With the leads attached to the crankshaft sensor, you should see a reading of about 0.5-1 volt. The sensor is most likely defective if the reading is much higher or lower than this. If your sensor is defective, you’ll need to replace it.
You should also check the voltage of the wiring harness by touching one lead to the sensor’s signal wire and the other lead to a ground source. If you get a low or fluctuating voltage, there could be an issue with the wiring and it will need to be repaired.
Step 9: Remove the ASD Relay
If your car has an ASD (automatic shut-off) relay, you’ll need to remove it before testing the crankshaft sensor. The ASD relay is usually located in the engine bay, and it’s easy to identify because it has a large black connector. To remove the ASD relay, disconnect it from the wiring harness.
If you skip this step, the ASD relay may prevent you from getting an accurate reading on your multimeter.
Step 10: Set the Multimeter to DC Volts
Once you’ve removed the ASD relay, you’ll need to set the multimeter to DC volts. This is usually done by turning the knob until it points to the VDC symbol. You can use the voltage setting if your multimeter doesn’t have a DC voltage setting. After setting the multimeter to DC voltage, press the button (if your multimeter has one) to switch from AC to DC voltage measurement. Make sure the multimeter is still set to the correct voltage range.
You’ll now need to connect the leads to the crankshaft sensor. The positive lead (red) should be attached to the signal wire, and the negative lead (black) should be attached to the ground. Refer to your car’s service manual if you’re unsure which wire it is.
Step 11: Start the Engine
Start the engine and check the voltage reading on the multimeter. A healthy crankshaft sensor should produce a voltage reading of 0.5-1 volt while the engine is running. If you get a low or fluctuating voltage, the sensor is likely defective.
You should also check the voltage of the wiring harness by touching one lead to the sensor’s signal wire and the other lead to a ground source. If you get a low or fluctuating voltage, there could be an issue with the wiring and it will need to be repaired.
Following these steps on how to check crank sensor with multimeter will help you accurately test your crankshaft sensor using a multimeter. It’s important to note that if you’re unsure about any of the steps, it’s best to consult your vehicle’s service manual or seek assistance from a professional mechanic. It’s also worth mentioning that a faulty crankshaft sensor can cause a variety of issues with your vehicle, such as engine stalling, poor acceleration, and difficulty starting the engine.
Do You Need to Take Help From a Mechanic to Check the Crank Sensor?
While it is possible to check the crankshaft sensor on your own, if you are not comfortable working with electrical systems or do not have experience using a multimeter, it may be best to seek the assistance of a mechanic. A mechanic will have the necessary knowledge and experience to accurately check and diagnose any issues with your car’s crankshaft sensor. Additionally, if you are unable to find the sensor or are unsure how to disconnect it from the wiring harness, a mechanic can help guide you through the process.
It is important to ensure that any repairs or replacements are done correctly, so if you have any doubts about performing this task on your own, it’s best to consult a professional. Remember to always prioritize safety and caution when working on your vehicle. If you are unsure or uncomfortable with any part of the process, it’s best to seek professional help.
Additional Tips and Advice:
1. Check the engine oil level and quality. If it’s low, top it off and change it.
2. Check for any loose or damaged wires going to the sensor.
3. Clean the crankshaft sensor and connector with contact cleaner or replace the sensor if necessary.
4. If your car has a mass airflow sensor, check that. A bad MAF sensor can cause similar symptoms.
5. If the problem is still not resolved, have the computer system scan for codes to see if there are any pending or stored codes that can help diagnose the issue.
6. If you replaced the sensor and the problem persists, the wiring or connector may be an issue. Have these inspected and repaired as necessary?
7. When testing your crankshaft sensor with a multimeter, check the resistance in both directions. Some sensors will have different readings in each direction.
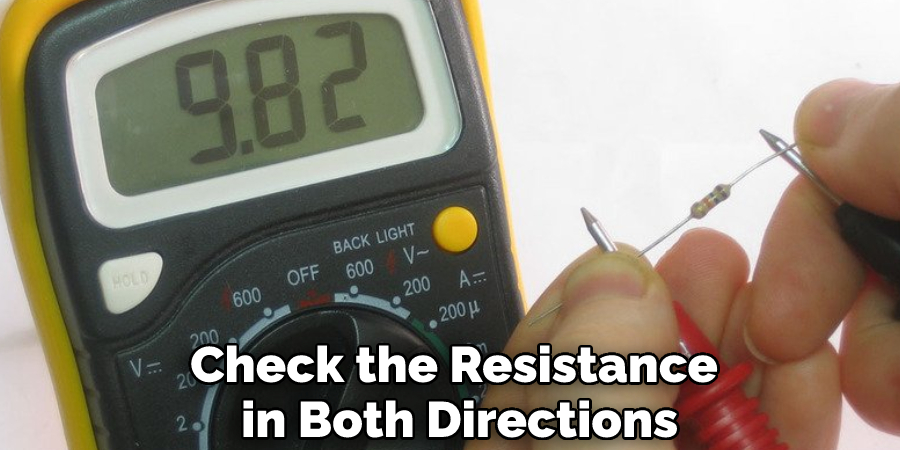
How Much Voltage Should a Crank Sensor Have?
As you already know, the crankshaft position sensor provides vital data to the engine control unit (ECU). The ECU uses this data to control ignition timing and fuel injection. The crankshaft position sensor produces a small AC voltage as it passes a magnetic field. The amount of voltage produced depends on the speed of the crankshaft.
The ECU uses the data from the crankshaft position sensor to determine engine speed and ignition timing. The ECU must know the crankshaft’s position to fire the spark plugs correctly. The engine will not run correctly if the crankshaft position sensor is not working properly.
You can check the crankshaft position sensor with a multimeter. The crankshaft position sensor produces a small AC voltage when it passes a magnetic field. You can check the crankshaft position sensor by connecting the multimeter to the sensor’s two wires. The multimeter should read about 0.5 volts when the engine is cranking. If the multimeter does not read this voltage, the crankshaft position sensor is not working properly.
You Can Check It Out To Remove Water Heater Element without Element Wrench
Can You Test the Crank Sensor With an Oscilloscope?
Yes, you can test the crank sensor with an oscilloscope. First, you can determine if the sensor is working properly by checking the signal’s waveform. Then, you can connect the lead of the oscilloscope to the sensor’s signal wire and ground the scope’s ground lead to the engine block.
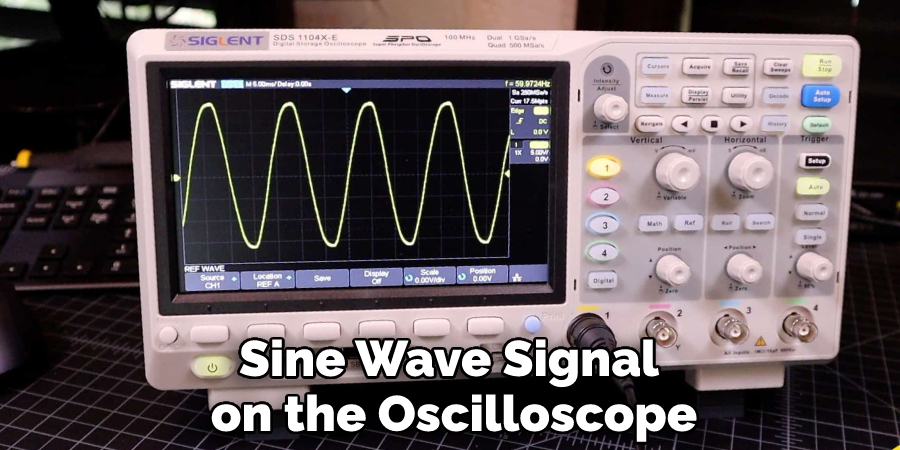
If the sensor works properly, you should see a sine wave signal on the oscilloscope. The amplitude of the signal will vary depending on the engine speed. If the signal is not a sine wave or there is no signal, then the sensor is most likely defective.
You Can Check It Out To Test Amplifier Output with Multimeter
Frequently Asked Questions:
Q: How Do I Know if My Crankshaft Sensor is Bad?
A: The most common symptoms of a bad or failing crankshaft position sensor include engine stalling, misfire, difficulty starting the engine, and loss of power while driving. You may also see the check engine light come on, and your car may not pass emissions testing. If you experience any of these symptoms, it’s best to test the crankshaft sensor with a multimeter.
Q: Can a Bad Crank Sensor Cause No Spark?
A: Yes, a bad crankshaft position sensor can cause no spark. The sensor sends data to the engine control unit, which uses this information to fire the spark plugs. If the sensor is not functioning correctly, the ECU will not know when to send a signal to fire the spark plugs, resulting in no spark.
Q: How Do You Check if a Crank Sensor is Getting Power?
A: To check if a crankshaft position sensor is getting power, you can use a multimeter. Set the multimeter to DC voltage and connect the leads to the sensor’s positive and negative terminals. Crank the engine, and if you see a reading of about 0.5-1 volt, it means that the sensor is getting power.
Q: Can You Drive with a Bad Crank Sensor?
A: It’s not recommended to drive with a bad crankshaft position sensor. If the sensor fails while driving, it can cause your engine to stall or lose power, potentially leading to a dangerous situation on the road. It’s best to have the sensor replaced as soon as possible to avoid any potential hazards.
Final Words
A crank sensor is an important part of the ignition system in a car. This sensor helps to detect when the engine is starting so that the appropriate fuel mixture can be delivered. However, if this sensor fails, it can cause car performance problems. This article has shown you how to check crank sensor with multimeter.
With the help of this article, you should now be able to diagnose a crank sensor issue on your vehicle. Please get in touch with a professional mechanic if you have any questions or need further assistance. Thanks for reading!
You Can Check It Out To Use a Fieldpiece Multimeter
Occupation: Expert in Hardware Tools
Education: Bachelor’s Degree in Mechanical Engineering
Profile:
Enrique Howard is a seasoned expert in the field of hardware tools, with a robust background in mechanical engineering that underpins his extensive knowledge and skills. Holding a degree in mechanical engineering, Enrique has cultivated a deep understanding of tool design, mechanics, and the intricacies of various hardware applications. His educational foundation empowers him to innovate and refine tools that enhance efficiency and effectiveness in a wide range of industries.
Professional Focus:
Enrique’s professional focus encompasses a diverse array of areas within the hardware tools sector, including:
- Tool Design and Development: Leveraging his engineering expertise, Enrique specializes in designing tools that meet specific user needs, ensuring optimal performance and durability.
- Material Science: Understanding the properties of various materials allows him to recommend the best tools for specific applications, enhancing safety and efficiency.
- Ergonomics: He emphasizes the importance of ergonomic design in tools, striving to create solutions that reduce user fatigue and improve comfort during prolonged use.
- Sustainability: Enrique is committed to promoting environmentally friendly practices in tool manufacturing, advocating for the use of sustainable materials and processes.
- Education and Training: Through workshops, seminars, and written content, he focuses on educating both professionals and DIY enthusiasts about tool selection, maintenance, and safe usage practices.
Throughout his career, Enrique has worked on numerous projects, collaborating with manufacturers and craftsmen to develop cutting-edge hardware solutions. His expertise spans from traditional hand tools to advanced power tools, allowing him to contribute significantly to both professional and DIY communities.
As an author, Enrique shares his insights through articles, guides, and tutorials, aimed at helping enthusiasts and professionals alike navigate the complexities of hardware tools. His passion for education and practical application drives him to continually explore new technologies and methodologies, making him a trusted voice in the hardware industry.
Whether he’s writing about the latest tool advancements or providing practical tips for tool maintenance, Enrique Howard is dedicated to empowering others with the knowledge and skills necessary to excel in their hardware endeavors.