When you’re dealing with a vintage car, it’s important to know how to bench test a distributor. This ensures that the distributor is in good working order and will help your car start and run correctly. In this blog post, we will walk you through the process of bench-testing a distributor so that you can determine whether or not it is defective. Let’s get started!
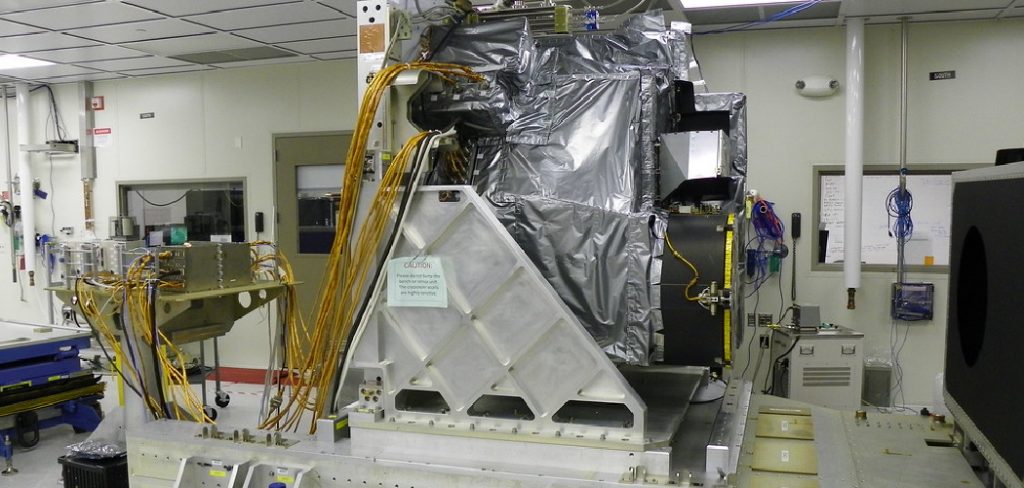
What Is a Vehicle Distributor?
A vehicle distributor is a device that distributes high voltage from the ignition coil to the spark plugs in the correct order. This ensures that the spark plugs fire in the correct sequence, providing the power needed to start the engine. The distributor is an essential part of any internal combustion engine and must be properly maintained to keep the engine running smoothly.
One way to ensure that the distributor is working properly is to check the points and replace them, if necessary, regularly. The points are what create the electrical connection between the coil and the spark plugs, and they can become worn over time. So, replacing them regularly will help keep your engine running like new.
Why Should You Bench Test a Distributor?
It’s always a good idea to bench test a distributor before installing it on your engine. This will ensure that the distributor is functioning properly and help you avoid potential issues. There are a few different ways to bench test a distributor, but the most important thing is ensuring a good connection between the distributor and the engine.
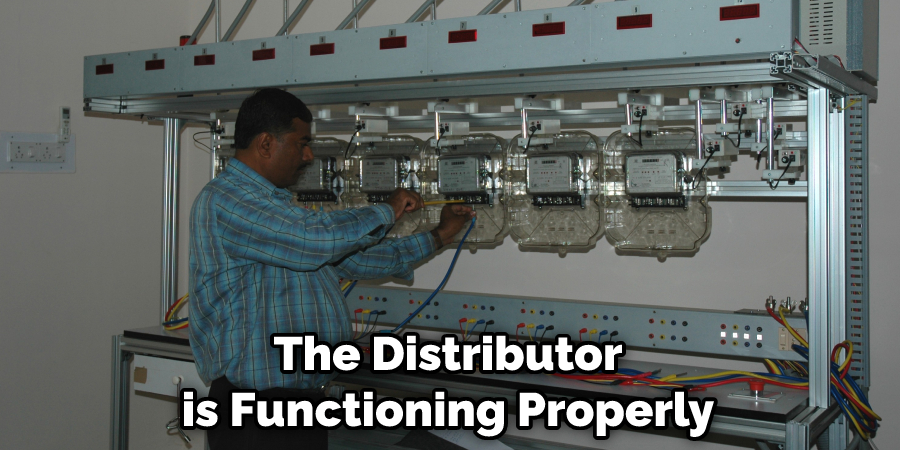
You’ll also want to ensure that the rotor is spinning correctly. Then, if everything looks good, you can install the distributor on your engine and enjoy peace of mind knowing it will work properly.
Needed Materials:
A Distributor Testing Machine:
To bench test a distributor, you will need a distributor testing machine. This is a specialized tool that can be found at most auto supply stores or online. It allows you to simulate the operation of a distributor and check for any issues before installing it on your engine.
A Multimeter:
You will also need a multimeter to accurately measure the voltage output of the distributor. This is an essential tool for any vehicle owner and can be found at most hardware or auto supply stores.
A 12-volt Power Source:
You will need a 12-volt power source to provide the necessary voltage for testing the distributor. This can be a car battery or a separate power supply. It’s important to ensure that you have a stable power source to get accurate results.
A Set of Spark Plugs:
Lastly, you will need a set of spark plugs to test the distributor’s output and make sure they are firing correctly. Make sure you use the correct type and size of spark plugs for your engine.
9 Tips to Follow on How to Bench Test a Distributor
When troubleshooting ignition issues, one of the first places to start is with the distributor. A quick and easy way to test the health of your distributor is to do a bench test.
1. Accurately Test the Dwell Angle
The dwell angle is how long the points are in contact with each other before they open back up. This is what creates the spark that ignites the air/fuel mixture in the cylinders. You’ll need a dwell meter to test this. Connect the meter’s leads to the points to test the dwell angle.
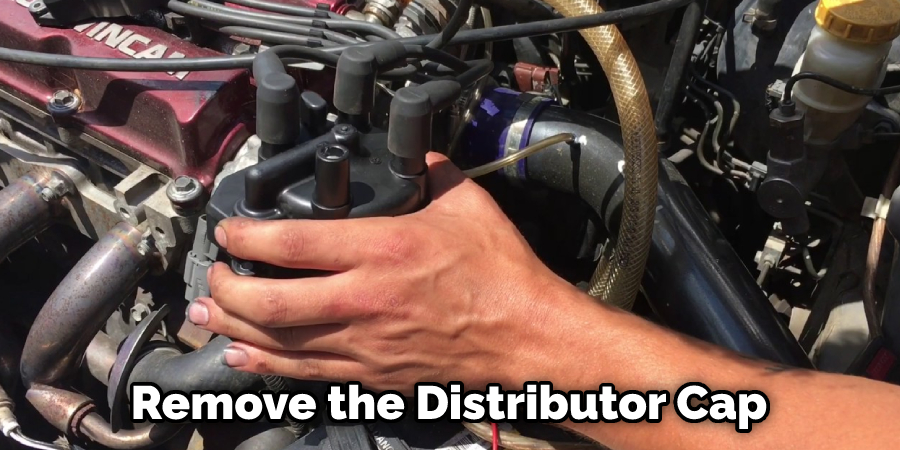
With the engine off, turn the distributor so that the points are just about to open. This is when you’ll get the most accurate reading. The dwell angle should be between 30-40 degrees. If it’s not within this range, it could be a sign that the points need to be replaced.
2. Check for Vacuum Advance
The vacuum advance is what helps the engine run more efficiently by advancing the spark timing. To check for the vacuum advance, you’ll need a vacuum gauge. Connect the gauge to the distributor’s vacuum advance port. With the engine off, turn on the ignition and let the gauge stabilize. Then, rev the engine and see how much vacuum is being created. If there isn’t enough vacuum, it could be a sign of a problem with the carburetor or intake manifold.
The vacuum advance should also hold steady as you rev the engine. If it drops, it could be a sign of a faulty distributor or other issues. You can also check the vacuum advance by using a hand-held vacuum pump to apply vacuum to the distributor. If it doesn’t move smoothly or sticks, it could be a sign that the advance mechanism is faulty and needs to be replaced.
3. Inspect the Distributor Shaft Play
With the engine off, remove the distributor cap and rotor. Then, grab hold of the distributor shaft and try to wiggle it back and forth. There should be very little play. If there’s too much play, it could be a sign that the bearings are worn out and need to be replaced.
You can also check the play by turning the rotor clockwise and counterclockwise. The rotor should move smoothly and without any hesitation.
4. Evaluate the Distributor Cap and Rotor
The distributor cap and rotor play an important role in the ignition process. Over time, they can become cracked or worn out, which can cause problems. Inspect both the distributor cap and rotor for any signs of damage. If either of them is damaged, it’s best to replace them.
You can also check the resistance of the rotor using a multimeter. Place one probe on the center electrode and the other on the metal arm. The reading should be between 6,000-35,000 ohms. If it’s not within this range, it could be a sign that the rotor is faulty and needs to be replaced.
5. Assess the Condition of the Points
The points are what create the spark that ignites the air/fuel mixture in the cylinders. Over time, they can become pitted or burned, which can cause problems. To check the condition of the points, remove the distributor cap and rotor. Then, inspect the points for any damage. If they’re damaged, it’s best to replace them.
But even if they don’t look damaged, it’s a good idea to replace them regularly. The points wear down over time and can cause problems with the ignition system. You can also check the resistance of the points using a multimeter. The reading should be between 0.3-1.5 ohms. If it’s not within this range, it could be a sign that the points are faulty and need to be replaced.
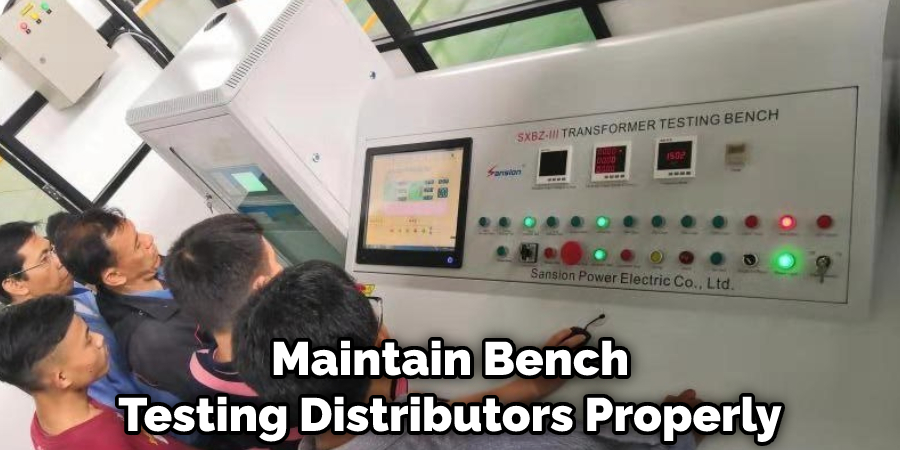
6. Test the Ignition Coil
The ignition coil is what transforms the low voltage from the battery into the high voltage needed to create a spark. To test the ignition coil, you’ll need an ohmmeter. With the engine off, disconnect the primary wire from the coil and attach the ohmmeter leads to the terminals. The resistance should be between 0.5 and 2 ohms. If it’s not within this range, it could be a sign that the coil needs to be replaced.
You can also test the secondary coil by connecting one ohmmeter lead to the positive terminal and the other lead to the high-tension wire. The resistance should be between 7,000-12,000 ohms. If it’s not within this range, it could be a sign that the secondary coil is faulty.
7. Swap Out the Spark Plugs
Spark plugs can become fouled or damaged over time, which can cause ignition issues. To check the condition of the spark plugs, remove them and inspect them for any damage. If they’re damaged, it’s best to replace them. You can also swap them out with a known working set to see if that resolves the issue.
The spark plug gap is also important for proper ignition. Use a feeler gauge to check the gap and adjust it if necessary. You can find the recommended gap in your vehicle’s manual. It’s also a good idea to replace the spark plugs regularly.
8. Test the Output Voltage
To test the output voltage of the distributor, you’ll need a multimeter. With the engine off, connect the positive lead of the multimeter to one of the distributor’s terminals and connect the negative lead to ground. Turn on the ignition and check the voltage output. It should be between 12-14 volts. If it’s not, there could be an issue with the distributor.
The ignition system is an integral part of your vehicle’s engine performance. By regularly testing and maintaining the components, you can ensure that your vehicle starts smoothly and runs efficiently. If you encounter any issues with the ignition system, it’s best to address them promptly to avoid any potential safety hazards or further damage to your vehicle.
9. Perform a Vacuum Test
Lastly, you can perform a vacuum test to ensure that the distributor is functioning properly. With the engine off, connect a vacuum gauge to one of the intake manifold ports and another to the distributor’s vacuum advance port. Start the engine and let it idle. The vacuum should increase as the engine speed increases. If there is no change in the vacuum, it could be a sign of a problem with the distributor.
By following these nine tips on how to bench test a distributor, you’ll be able to accurately diagnose any issues and get your car back on the road in no time.
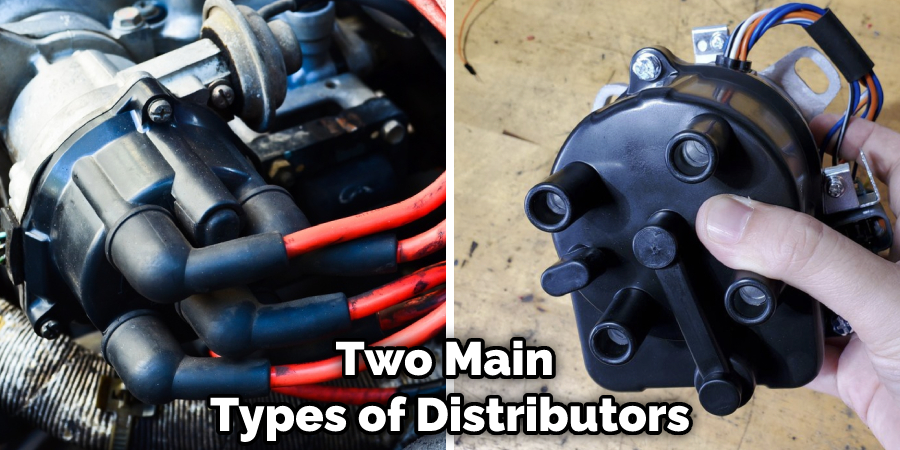
10 Signs You’re Not Bench-Testing Your Distributors Enough
As any seasoned mechanic knows, bench testing your distributors is crucial to maintaining a well-running engine. However, many novice mechanics overlook this important step, leading to distributor failure and engine trouble down the road. Here are ten signs that you do not test your distributors enough:
1. You’re not familiar with the symptoms of distributor failure.
2. You’ve never stripped down a distributor to clean and inspect it.
3. You don’t have a distributor bench tester in your shop.
4. You’ve never checked the dwell angle on your distributor.
5. You don’t know how to adjust the points gap on your distributor.
6. You’ve never checked the rotor or cap for wear and tear.
7. You don’t know how to test the ignition coil on your distributor.
8. You’ve never replaced the spark plug wires on your distributor.
9. You don’t know how to test the mechanical advance on your distributor.
10. You’ve never rebuilt a distributor from scratch.
If you can’t check off all these boxes, it’s time to start giving your distributors more attention! By taking the time to maintain them properly, you can save yourself a lot of headaches (and money) down the road.
What to Look for When Bench Testing a Distributor
Before installing a new distributor in your car, you’ll want to bench test it to ensure it’s working properly. The first step is to remove the distributor cap and rotor. Next, a voltmeter is used to test the coil for continuity. If there’s no continuity, the coil needs to be replaced. Once you’ve confirmed that the coil is in working order, reconnect the rotor and distributor cap.
Finally, turn the engine over by hand and observe the distributor shaft. It should rotate smoothly without any wobbling or binding. If everything looks good, then you can be confident that your new distributor will work properly when installed in your car. Keep reading for more information about how to bench test a distributor.
The Importance of Bench Testing a Distributor
Before a distributor is installed in an engine, it must be tested to ensure proper fit and function. This process is known as bench testing, and it involves checking the distributor for correct timing, advance curves, and dwell angles. Bench testing is essential for any engine rebuild, as it helps to ensure that the distributor will work correctly once installed.
In addition, bench testing can also help identify potential problems that may need to be addressed before installation. By taking the time to bench test a distributor, you can help to ensure a successful engine rebuild.
What to Consider when Bench Testing a Distributor
When you need to test a distributor, you want to be sure that the results are accurate. Here are a few factors to consider when bench-testing a distributor:
The first thing to consider is the timing of the distributor. You’ll want to ensure that the timing is set correctly to get accurate results. If the timing is off, it can throw off the test results.
Another thing to consider is the type of distributor you’re testing. There are two main types of distributors: point distributors and electronic distributors. Each type of distributor requires a different type of test, so be sure you know which type you’re testing before you begin.
Finally, ensure you have all the proper tools and supplies before you begin your test. Having everything you need will help ensure that the test goes smoothly and that you get accurate results.
Frequently Asked Questions:
Q: How Often Should I Bench Test My Distributor?
A: It’s recommended to bench test your distributor every time you rebuild or replace it, and at least once a year as part of regular maintenance. You should also bench-test it if you experience any issues with your engine’s performance. It’s better to catch any potential issues early on rather than wait for a major problem to occur. The more you bench-test your distributor, the better understanding you’ll have of its overall condition.
Q: Can I Bench Test My Own Distributor, or Do I Need a Professional?
A: It is possible to bench test your own distributor with the proper tools and knowledge. However, if you’re not confident in your abilities or don’t have access to the necessary equipment, it’s best to have a professional mechanic perform the test for you. This will ensure accurate results and proper handling of delicate parts. It’s always better to be safe than sorry when it comes to your vehicle’s performance.
Q: Can Bench Testing Prevent Distributor Failure?
A: While bench testing cannot guarantee that your distributor won’t fail, it can help identify potential issues early on. By catching problems before they become bigger, you can prevent serious engine damage and costly repairs. Regular bench testing and maintenance can also extend the lifespan of your distributor, saving you time and money in the long run. So, while it may not completely prevent failure, bench testing is a valuable tool in maintaining your vehicle’s performance.
Q: Is Bench Testing Necessary for Electronic Distributors?
A: Yes, bench testing is still necessary for electronic distributors. While they may not have points and condensers like traditional distributors, they still require proper timing and advanced curves to function correctly. It’s important to follow the manufacturer’s instructions for bench-testing electronic distributors and use the appropriate equipment to ensure accurate results.
Conclusion
Now that you know how to bench test a distributor, you can troubleshoot any issues you may have with your car’s ignition system. This simple test will save you time and money by pinpointing the problem so you can fix it quickly and get back on the road.
You Can Check It Out To Use a Greenlee Multimeter
You Can Check it Out to Use a Fieldpiece Multimeter
Occupation: Expert in Hardware Tools
Education: Bachelor’s Degree in Mechanical Engineering
Profile:
Enrique Howard is a seasoned expert in the field of hardware tools, with a robust background in mechanical engineering that underpins his extensive knowledge and skills. Holding a degree in mechanical engineering, Enrique has cultivated a deep understanding of tool design, mechanics, and the intricacies of various hardware applications. His educational foundation empowers him to innovate and refine tools that enhance efficiency and effectiveness in a wide range of industries.
Professional Focus:
Enrique’s professional focus encompasses a diverse array of areas within the hardware tools sector, including:
- Tool Design and Development: Leveraging his engineering expertise, Enrique specializes in designing tools that meet specific user needs, ensuring optimal performance and durability.
- Material Science: Understanding the properties of various materials allows him to recommend the best tools for specific applications, enhancing safety and efficiency.
- Ergonomics: He emphasizes the importance of ergonomic design in tools, striving to create solutions that reduce user fatigue and improve comfort during prolonged use.
- Sustainability: Enrique is committed to promoting environmentally friendly practices in tool manufacturing, advocating for the use of sustainable materials and processes.
- Education and Training: Through workshops, seminars, and written content, he focuses on educating both professionals and DIY enthusiasts about tool selection, maintenance, and safe usage practices.
Throughout his career, Enrique has worked on numerous projects, collaborating with manufacturers and craftsmen to develop cutting-edge hardware solutions. His expertise spans from traditional hand tools to advanced power tools, allowing him to contribute significantly to both professional and DIY communities.
As an author, Enrique shares his insights through articles, guides, and tutorials, aimed at helping enthusiasts and professionals alike navigate the complexities of hardware tools. His passion for education and practical application drives him to continually explore new technologies and methodologies, making him a trusted voice in the hardware industry.
Whether he’s writing about the latest tool advancements or providing practical tips for tool maintenance, Enrique Howard is dedicated to empowering others with the knowledge and skills necessary to excel in their hardware endeavors.